Everything you need to know about back-ordering
Back-ordering is a term you have probably heard before, especially if you regularly make online purchases.

Everything you need to know about back-ordering
Back-ordering is a term you have probably heard before, especially if you regularly make online purchases.

Everything you need to know about back-ordering
Back-ordering is a term you have probably heard before, especially if you regularly make online purchases.

Everything you need to know about back-ordering
Back-ordering is a term you have probably heard before, especially if you regularly make online purchases.

View all blogs
11 juni 2024
Back-ordering is a term you have probably heard before, especially if you regularly make online purchases. But what does it actually mean? And why is it so important in the supply chain? In this article, I will tell you everything you need to know about back-ordering.
What is back-ordering?
To start, let’s look at the definition and basic concept of back-ordering. Back-ordering refers to a situation where a product you have ordered is not immediately in stock and, therefore, cannot be delivered right away. Instead, the order is placed in a waiting status until the product is back in stock and can be shipped.
This can have various reasons. Perhaps the demand for the product is higher than expected, or the supplier is facing logistical challenges. Whatever the reason, back-ordering is a way to ensure that customers ultimately receive the desired product, even if it is not available at the time of ordering.
Definition and basic concept of back-ordering
To get a clear picture of back-ordering, it is important to understand how this process works within a company's supply chain. It all starts with linking carriers and sales channels to a system like ShopLinkr. By making this connection, orders from a sales channel can be processed with the labels of a carrier.
When an order is placed and the product is out of stock, the order is marked as a back-order. The system keeps track of which products and how many of them still need to be delivered. Once the product is back in stock, the order can be executed and shipped to the customer.
The importance of back-ordering in the supply chain
Back-ordering plays a crucial role in a company's supply chain. It enables companies to meet customer demand, even when they do not have sufficient stock at that moment. This helps retain customers and prevents them from turning to competitors in search of the desired product.
Moreover, back-ordering allows companies to manage their inventory efficiently. Instead of holding excessive stock, they can order just enough products to meet demand. This saves costs and reduces waste.
How does back-ordering work?
Now that you have an idea of what back-ordering is and why it is important, let’s take a look at the process of back-ordering and the factors that may influence its efficiency.
The back-ordering process step by step
The back-ordering process typically proceeds in several steps. First, the order is placed and checked for availability. If the product is not in stock, it is labeled as a back-order, and the customer is informed of the expected delivery time.
Next, the product is reordered from the supplier or manufacturer. The delivery is then awaited, and once the product arrives, it is processed and shipped to the customer. It is important to manage the entire process well to ensure that customers are informed in a timely manner and remain satisfied.
Factors that affect the efficiency of back-ordering
While back-ordering can be a useful process, there are also factors that can affect its efficiency. One of the most important factors is communication. It is essential to inform customers clearly and promptly about the status of their back-order. This helps avoid frustration and ensures transparency.
Another factor is the reliability of the supplier. If the supplier is unable to fulfill the order within a reasonable timeframe, this can lead to delays and dissatisfied customers. It is important to work with reliable suppliers who can meet the demand.
Advantages and disadvantages of back-ordering
Back-ordering can have both advantages and disadvantages for businesses. Let’s take a look at how it can help and what potential challenges and risks there may be.
How back-ordering can help businesses
Back-ordering offers various advantages for businesses. It allows them to keep customers satisfied by giving them the possibility to receive the desired product, even if it is not immediately available. Additionally, businesses can efficiently manage their inventory and reduce waste using back-ordering.
Potential challenges and risks of back-ordering
Of course, there are also some challenges and risks associated with back-ordering. Delivery delays and unclear communication can lead to customer dissatisfaction. Moreover, managing back-orders can be a complex process that requires accurate planning and attention.
Back-ordering strategies for businesses
To effectively manage back-ordering, businesses can utilize various strategies. Here are some tips for effectively managing back-orders.
Tips for effectively managing back-orders
Ensure clear communication with customers about the status of their back-order.
Collaborate with reliable suppliers who can meet the demand.
Monitor and manage inventory accurately to prevent back-orders from lasting too long.
Set realistic expectations for customers and communicate any delays as soon as possible.
Choosing the right back-ordering strategy for your business
Every business is unique, so it is important to choose the right back-ordering strategy that fits your specific needs. For example, you might decide to only accept back-orders for certain products or to maintain a minimum stock level to reduce back-orders. It is essential to evaluate which strategy works best for your business and continuously optimize it.
Frequently asked questions about back-ordering
When it comes to back-ordering, there are often some common questions and misconceptions. Let’s answer some of these questions.
Answers to common questions about back-ordering
What happens if a back-order cannot be fulfilled? In this case, the customer is usually informed and can choose to cancel the order or wait for the product.
Can back-orders be canceled? Yes, it is possible to cancel a back-order, but this must be done in a timely manner before the order is processed and shipped.
Debunking misconceptions about back-ordering
Back-ordering is not the same as a delivery delay. It simply means that the product is not immediately available but will be delivered later.
Back-ordering is not a sign of poor service. It is a way to help customers receive the desired product, even if it is temporarily out of stock.
With this information, you hopefully have a better understanding of back-ordering and the role it plays in a company's supply chain. Whether you are a customer dealing with back-orders or a business owner wanting to implement back-ordering, it is important to understand and effectively manage the process to ensure a positive experience.
After reading this article about back-ordering, do you feel that your inventory and order management could use a boost? With ShopLinkr, you can effortlessly keep track of your inventory and process orders in no time. And the best part: you can try it for 14 days completely free. Experience for yourself how easy it is to manage everything in one place and how our connections with the most well-known and reliable companies take your webshop to the next level. Try ShopLinkr now for 14 days free and say goodbye to back-order headaches!
Back-ordering is a term you have probably heard before, especially if you regularly make online purchases. But what does it actually mean? And why is it so important in the supply chain? In this article, I will tell you everything you need to know about back-ordering.
What is back-ordering?
To start, let’s look at the definition and basic concept of back-ordering. Back-ordering refers to a situation where a product you have ordered is not immediately in stock and, therefore, cannot be delivered right away. Instead, the order is placed in a waiting status until the product is back in stock and can be shipped.
This can have various reasons. Perhaps the demand for the product is higher than expected, or the supplier is facing logistical challenges. Whatever the reason, back-ordering is a way to ensure that customers ultimately receive the desired product, even if it is not available at the time of ordering.
Definition and basic concept of back-ordering
To get a clear picture of back-ordering, it is important to understand how this process works within a company's supply chain. It all starts with linking carriers and sales channels to a system like ShopLinkr. By making this connection, orders from a sales channel can be processed with the labels of a carrier.
When an order is placed and the product is out of stock, the order is marked as a back-order. The system keeps track of which products and how many of them still need to be delivered. Once the product is back in stock, the order can be executed and shipped to the customer.
The importance of back-ordering in the supply chain
Back-ordering plays a crucial role in a company's supply chain. It enables companies to meet customer demand, even when they do not have sufficient stock at that moment. This helps retain customers and prevents them from turning to competitors in search of the desired product.
Moreover, back-ordering allows companies to manage their inventory efficiently. Instead of holding excessive stock, they can order just enough products to meet demand. This saves costs and reduces waste.
How does back-ordering work?
Now that you have an idea of what back-ordering is and why it is important, let’s take a look at the process of back-ordering and the factors that may influence its efficiency.
The back-ordering process step by step
The back-ordering process typically proceeds in several steps. First, the order is placed and checked for availability. If the product is not in stock, it is labeled as a back-order, and the customer is informed of the expected delivery time.
Next, the product is reordered from the supplier or manufacturer. The delivery is then awaited, and once the product arrives, it is processed and shipped to the customer. It is important to manage the entire process well to ensure that customers are informed in a timely manner and remain satisfied.
Factors that affect the efficiency of back-ordering
While back-ordering can be a useful process, there are also factors that can affect its efficiency. One of the most important factors is communication. It is essential to inform customers clearly and promptly about the status of their back-order. This helps avoid frustration and ensures transparency.
Another factor is the reliability of the supplier. If the supplier is unable to fulfill the order within a reasonable timeframe, this can lead to delays and dissatisfied customers. It is important to work with reliable suppliers who can meet the demand.
Advantages and disadvantages of back-ordering
Back-ordering can have both advantages and disadvantages for businesses. Let’s take a look at how it can help and what potential challenges and risks there may be.
How back-ordering can help businesses
Back-ordering offers various advantages for businesses. It allows them to keep customers satisfied by giving them the possibility to receive the desired product, even if it is not immediately available. Additionally, businesses can efficiently manage their inventory and reduce waste using back-ordering.
Potential challenges and risks of back-ordering
Of course, there are also some challenges and risks associated with back-ordering. Delivery delays and unclear communication can lead to customer dissatisfaction. Moreover, managing back-orders can be a complex process that requires accurate planning and attention.
Back-ordering strategies for businesses
To effectively manage back-ordering, businesses can utilize various strategies. Here are some tips for effectively managing back-orders.
Tips for effectively managing back-orders
Ensure clear communication with customers about the status of their back-order.
Collaborate with reliable suppliers who can meet the demand.
Monitor and manage inventory accurately to prevent back-orders from lasting too long.
Set realistic expectations for customers and communicate any delays as soon as possible.
Choosing the right back-ordering strategy for your business
Every business is unique, so it is important to choose the right back-ordering strategy that fits your specific needs. For example, you might decide to only accept back-orders for certain products or to maintain a minimum stock level to reduce back-orders. It is essential to evaluate which strategy works best for your business and continuously optimize it.
Frequently asked questions about back-ordering
When it comes to back-ordering, there are often some common questions and misconceptions. Let’s answer some of these questions.
Answers to common questions about back-ordering
What happens if a back-order cannot be fulfilled? In this case, the customer is usually informed and can choose to cancel the order or wait for the product.
Can back-orders be canceled? Yes, it is possible to cancel a back-order, but this must be done in a timely manner before the order is processed and shipped.
Debunking misconceptions about back-ordering
Back-ordering is not the same as a delivery delay. It simply means that the product is not immediately available but will be delivered later.
Back-ordering is not a sign of poor service. It is a way to help customers receive the desired product, even if it is temporarily out of stock.
With this information, you hopefully have a better understanding of back-ordering and the role it plays in a company's supply chain. Whether you are a customer dealing with back-orders or a business owner wanting to implement back-ordering, it is important to understand and effectively manage the process to ensure a positive experience.
After reading this article about back-ordering, do you feel that your inventory and order management could use a boost? With ShopLinkr, you can effortlessly keep track of your inventory and process orders in no time. And the best part: you can try it for 14 days completely free. Experience for yourself how easy it is to manage everything in one place and how our connections with the most well-known and reliable companies take your webshop to the next level. Try ShopLinkr now for 14 days free and say goodbye to back-order headaches!
Back-ordering is a term you have probably heard before, especially if you regularly make online purchases. But what does it actually mean? And why is it so important in the supply chain? In this article, I will tell you everything you need to know about back-ordering.
What is back-ordering?
To start, let’s look at the definition and basic concept of back-ordering. Back-ordering refers to a situation where a product you have ordered is not immediately in stock and, therefore, cannot be delivered right away. Instead, the order is placed in a waiting status until the product is back in stock and can be shipped.
This can have various reasons. Perhaps the demand for the product is higher than expected, or the supplier is facing logistical challenges. Whatever the reason, back-ordering is a way to ensure that customers ultimately receive the desired product, even if it is not available at the time of ordering.
Definition and basic concept of back-ordering
To get a clear picture of back-ordering, it is important to understand how this process works within a company's supply chain. It all starts with linking carriers and sales channels to a system like ShopLinkr. By making this connection, orders from a sales channel can be processed with the labels of a carrier.
When an order is placed and the product is out of stock, the order is marked as a back-order. The system keeps track of which products and how many of them still need to be delivered. Once the product is back in stock, the order can be executed and shipped to the customer.
The importance of back-ordering in the supply chain
Back-ordering plays a crucial role in a company's supply chain. It enables companies to meet customer demand, even when they do not have sufficient stock at that moment. This helps retain customers and prevents them from turning to competitors in search of the desired product.
Moreover, back-ordering allows companies to manage their inventory efficiently. Instead of holding excessive stock, they can order just enough products to meet demand. This saves costs and reduces waste.
How does back-ordering work?
Now that you have an idea of what back-ordering is and why it is important, let’s take a look at the process of back-ordering and the factors that may influence its efficiency.
The back-ordering process step by step
The back-ordering process typically proceeds in several steps. First, the order is placed and checked for availability. If the product is not in stock, it is labeled as a back-order, and the customer is informed of the expected delivery time.
Next, the product is reordered from the supplier or manufacturer. The delivery is then awaited, and once the product arrives, it is processed and shipped to the customer. It is important to manage the entire process well to ensure that customers are informed in a timely manner and remain satisfied.
Factors that affect the efficiency of back-ordering
While back-ordering can be a useful process, there are also factors that can affect its efficiency. One of the most important factors is communication. It is essential to inform customers clearly and promptly about the status of their back-order. This helps avoid frustration and ensures transparency.
Another factor is the reliability of the supplier. If the supplier is unable to fulfill the order within a reasonable timeframe, this can lead to delays and dissatisfied customers. It is important to work with reliable suppliers who can meet the demand.
Advantages and disadvantages of back-ordering
Back-ordering can have both advantages and disadvantages for businesses. Let’s take a look at how it can help and what potential challenges and risks there may be.
How back-ordering can help businesses
Back-ordering offers various advantages for businesses. It allows them to keep customers satisfied by giving them the possibility to receive the desired product, even if it is not immediately available. Additionally, businesses can efficiently manage their inventory and reduce waste using back-ordering.
Potential challenges and risks of back-ordering
Of course, there are also some challenges and risks associated with back-ordering. Delivery delays and unclear communication can lead to customer dissatisfaction. Moreover, managing back-orders can be a complex process that requires accurate planning and attention.
Back-ordering strategies for businesses
To effectively manage back-ordering, businesses can utilize various strategies. Here are some tips for effectively managing back-orders.
Tips for effectively managing back-orders
Ensure clear communication with customers about the status of their back-order.
Collaborate with reliable suppliers who can meet the demand.
Monitor and manage inventory accurately to prevent back-orders from lasting too long.
Set realistic expectations for customers and communicate any delays as soon as possible.
Choosing the right back-ordering strategy for your business
Every business is unique, so it is important to choose the right back-ordering strategy that fits your specific needs. For example, you might decide to only accept back-orders for certain products or to maintain a minimum stock level to reduce back-orders. It is essential to evaluate which strategy works best for your business and continuously optimize it.
Frequently asked questions about back-ordering
When it comes to back-ordering, there are often some common questions and misconceptions. Let’s answer some of these questions.
Answers to common questions about back-ordering
What happens if a back-order cannot be fulfilled? In this case, the customer is usually informed and can choose to cancel the order or wait for the product.
Can back-orders be canceled? Yes, it is possible to cancel a back-order, but this must be done in a timely manner before the order is processed and shipped.
Debunking misconceptions about back-ordering
Back-ordering is not the same as a delivery delay. It simply means that the product is not immediately available but will be delivered later.
Back-ordering is not a sign of poor service. It is a way to help customers receive the desired product, even if it is temporarily out of stock.
With this information, you hopefully have a better understanding of back-ordering and the role it plays in a company's supply chain. Whether you are a customer dealing with back-orders or a business owner wanting to implement back-ordering, it is important to understand and effectively manage the process to ensure a positive experience.
After reading this article about back-ordering, do you feel that your inventory and order management could use a boost? With ShopLinkr, you can effortlessly keep track of your inventory and process orders in no time. And the best part: you can try it for 14 days completely free. Experience for yourself how easy it is to manage everything in one place and how our connections with the most well-known and reliable companies take your webshop to the next level. Try ShopLinkr now for 14 days free and say goodbye to back-order headaches!
Schedule a free demo
Clear explanation (1-on-1)
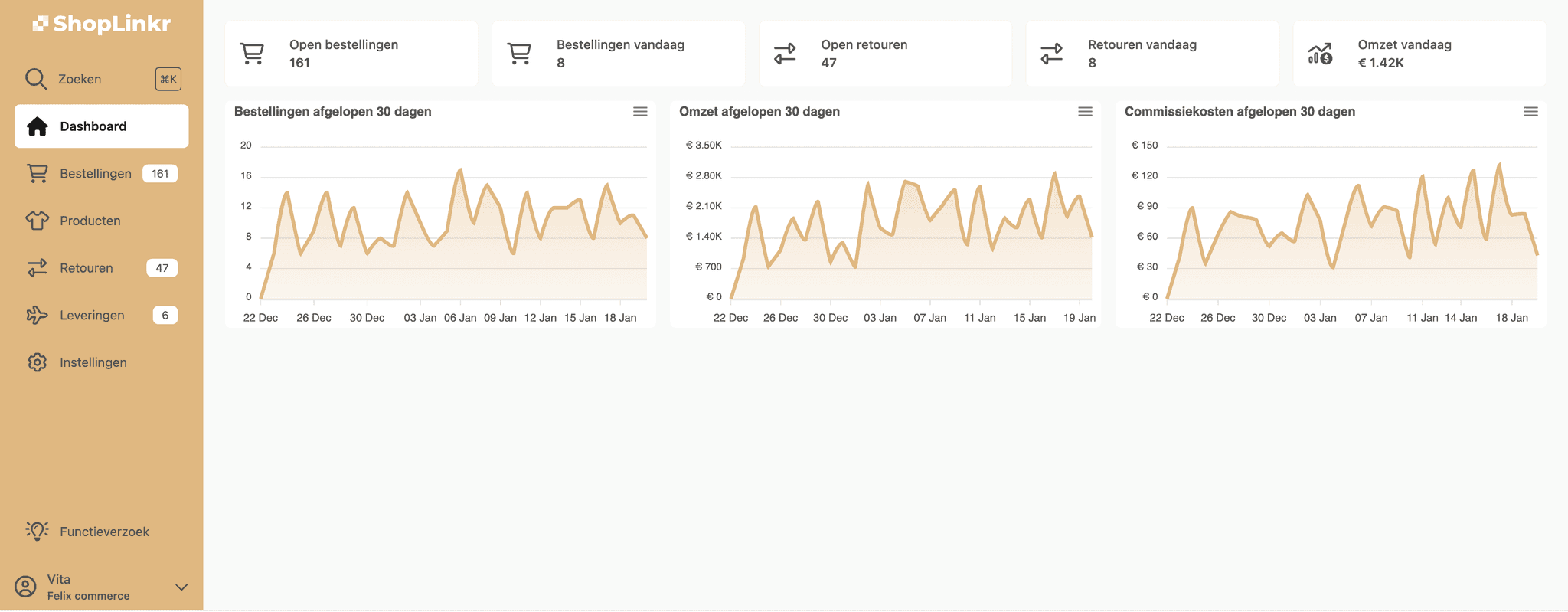
Do you want to always be informed of our latest developments?
Sign up for the newsletter.
Easily terminable
Always up-to-date
Schedule a free demo
Clear explanation (1-on-1)
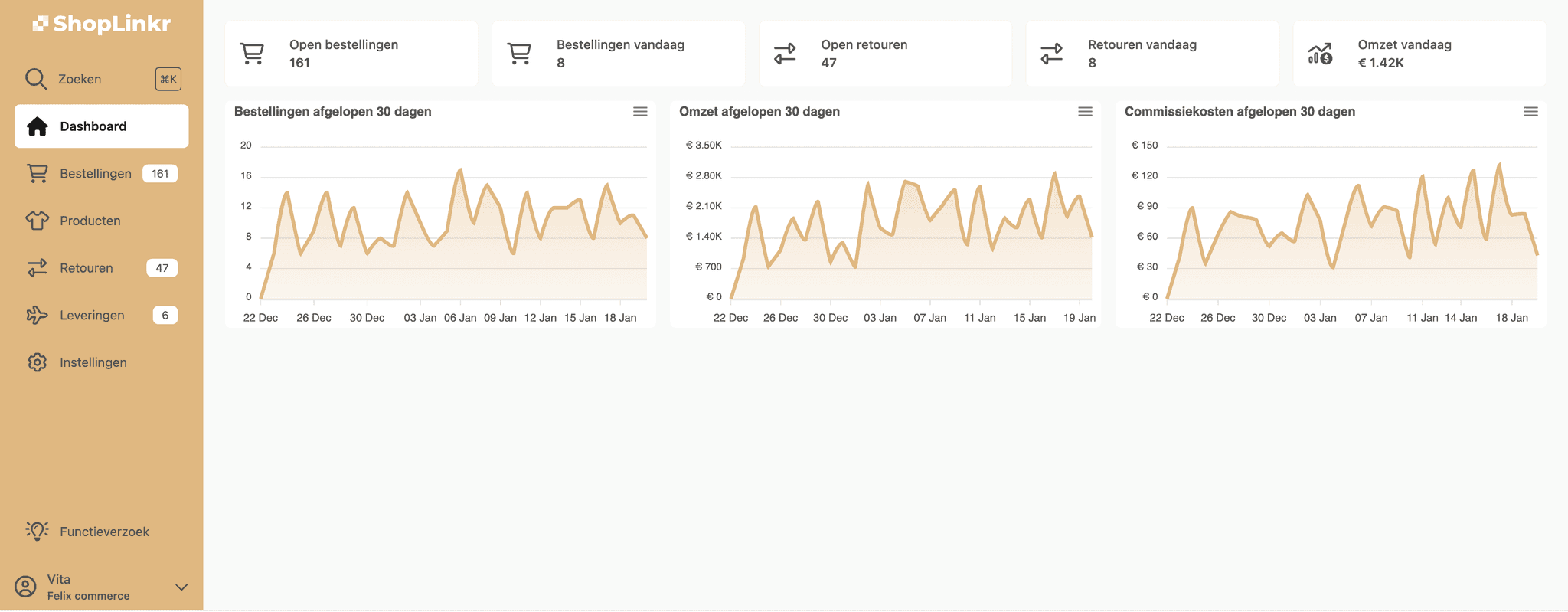
Do you want to always be informed of our latest developments?
Sign up for the newsletter.
Easily terminable
Always up-to-date
Schedule a free demo
Clear explanation (1-on-1)
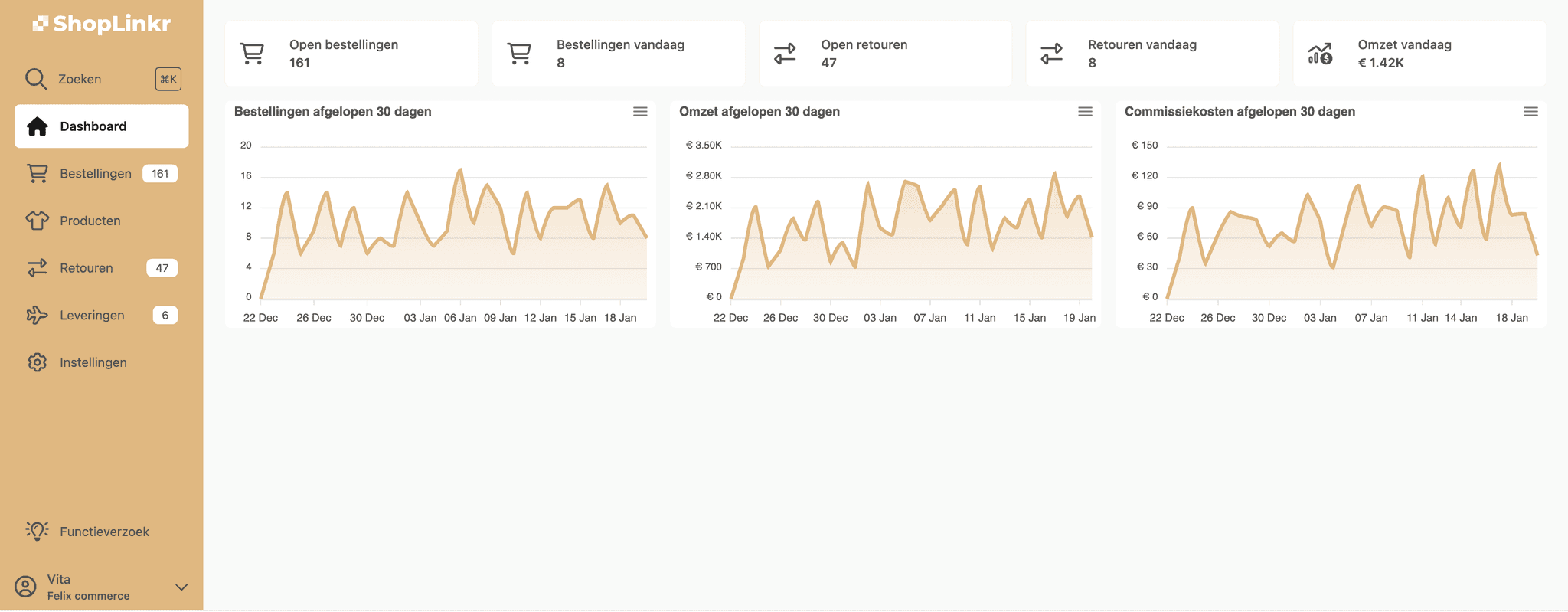
Do you want to always be informed of our latest developments?
Sign up for the newsletter.
Easily terminable
Always up-to-date
Schedule a free demo
Clear explanation (1-on-1)
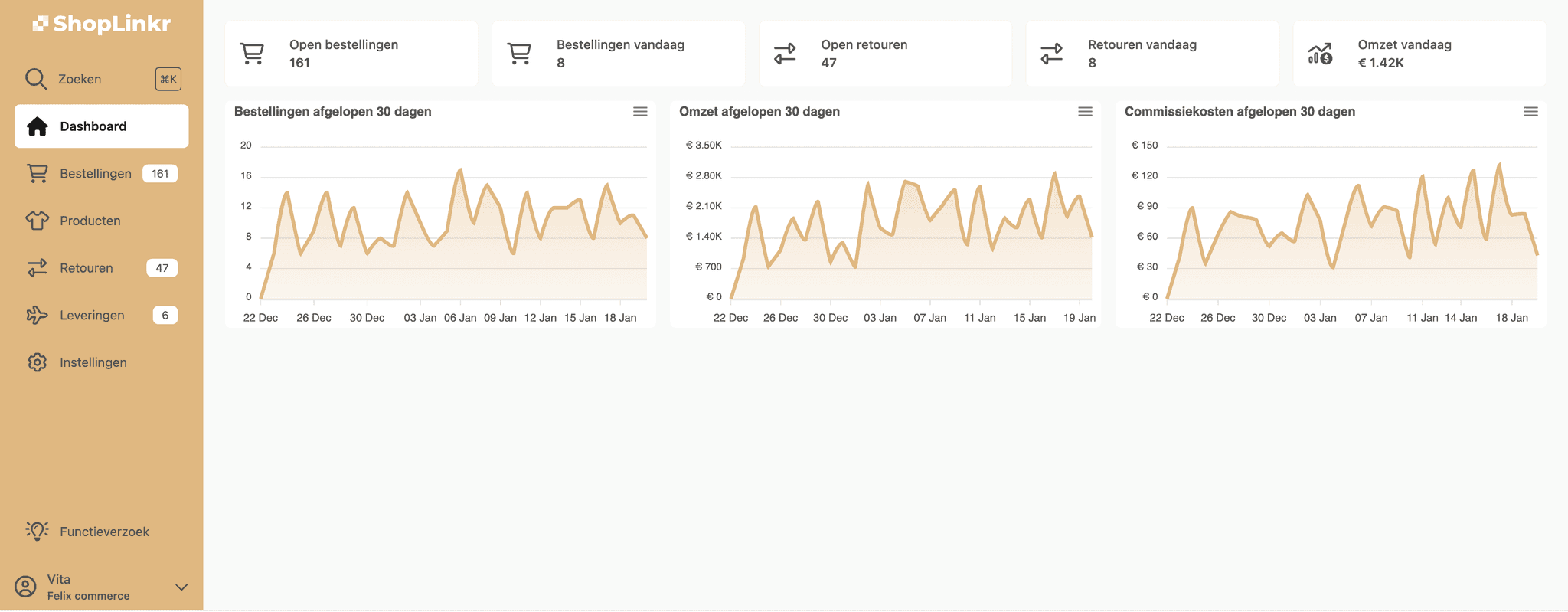
Do you want to always be informed of our latest developments?
Sign up for the newsletter.
Easily terminable
Always up-to-date